From rocket engines to all kinds of maritime hair, have countries been smashed "card necks"? This is a big proposition and a small proposition. First of all, let's talk about the Long March. As we all know, the Long March 9 carrier rocket is a new generation of heavy rockets being developed in China. It is a "sci-fi level" and will be used for deep space exploration, manned moon landing and fire, space infrastructure construction, etc. First flight between 2028 and 2030. This, time, and a little bit, let us first look at the exciting news of the neighborhood. According to Zhang Zhi, chief designer of the Long March 9 rocket, as a member of China's new generation of launch vehicles, the Long March 9 will be introduced to everyone at this year's Zhuhai Air Show. In this regard, the author wants to talk about aviation engines.
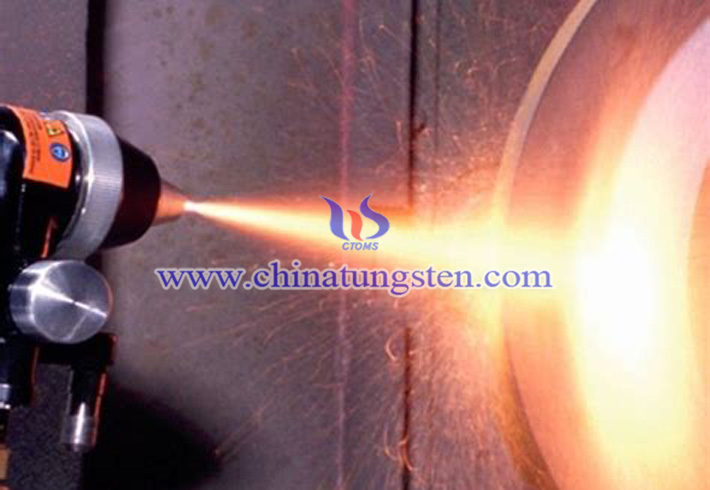
electron beam weld titanium alloy injector for rocket engine picture
As you may know, not only the rocket engine, but all aero engines need to have high temperature resistance and creep resistance. The more familiar airfare should be the turbofan engine in gas turbine engines, such as turbofan-15 (WS-15) and so on.
Without the support of high-temperature resistant alloy materials, even if it is a "power heart", it can't be moved. Speaking of this, we have to talk about one of China's superalloy pioneers - Shi Changxu. He is a famous material scientist in China, a senior academician of the Chinese Academy of Sciences and the Chinese Academy of Engineering, and a winner of the National Science and Technology Award. He developed China's first iron-based superalloy, and led the development of China's first generation of air-cooled cast nickel-based superalloy turbine blades, as well as heat-resistant, low-temperature materials and magnet-free manganese-aluminum austenitic steels. It is groundbreaking.
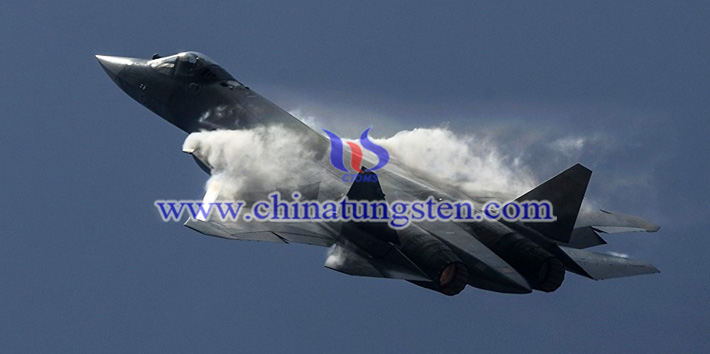
J-20 picture
Not long ago, the only countries in the world that could independently develop high-performance airfades were only a few countries such as the United States, Russia, Britain and France. The high technical threshold of Airfa is mainly due to the difficulty in many countries to break through the aviation materials. Aerospace requires engine materials to be very specific. According to earlier Russian media reports, China has solved the WS-15 airfare material problem and overcome the last difficulty. In the near future, all advanced engines are expected to be self-sufficient.
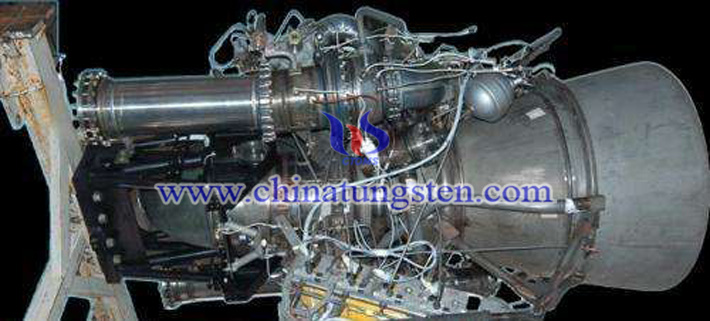
liquid oxygen kerosene engine picture
Although it is reported that the WS-15 has a single crystal crucible added to the blade, it can withstand a high temperature of 1700 ° C without melting. However, tungsten is still very popular. For example, tungsten carbide wear-resistant coatings and tantalum-tungsten alloy coatings can be used as surface coating materials for engine blades, thereby greatly improving the high temperature and wear resistance of the engine base. Corrosion and impact resistance. That is to say, for aviation hair, although tungsten occupies the weight of “l(fā)ight as a feather”, it plays the role of “heavy as a mountain” – improving the performance of the engine and prolonging its life.

presume J-20 equipped with WS 15 engine picture
In addition, although tungsten can not be the main component of the "power heart", it can still appear as a "scalpel". For example, a large number of high-precision carbide tools are used in the processing and manufacturing of aerial hair. Tungsten is also suitable for lubricant additives that are extremely important to Aerospace. In addition to the above information obtained by the author from the public data, in fact, the description of tungsten in the air is not particularly large. Of course, if the materials of several important parts of the airfare are known, for example, the tungsten alloy rotating shaft, the tungsten alloy weight on the rocker speed controller, and the tungsten alloy weight on the fuel regulating transfer controller.
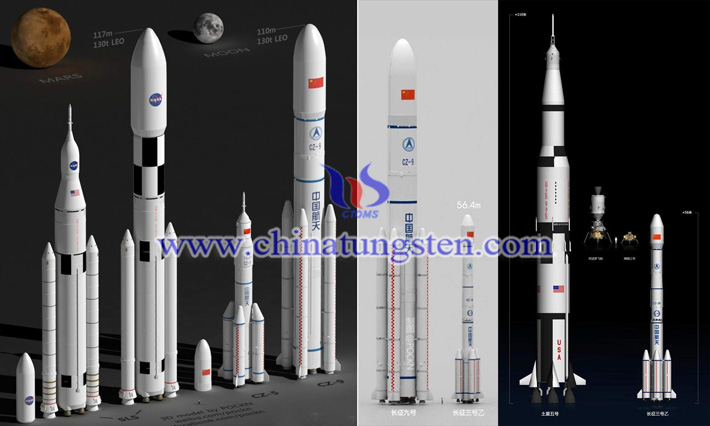
presume J-20 equipped with WS 15 engine picture
It can be seen that from rocket engines to various types of airfare, countries have encountered material bottlenecks. Of course, the processing technology is also a big difficulty. A short life span is a hard injury, which can be improved by materials. The processing technology of the blades on the airfare needs to be specially designed. This is a process of interlocking and inseparable, so which link must be incomparably correct. That is to say, the level of aeronautical processing in a country can be roughly judged from the blade.
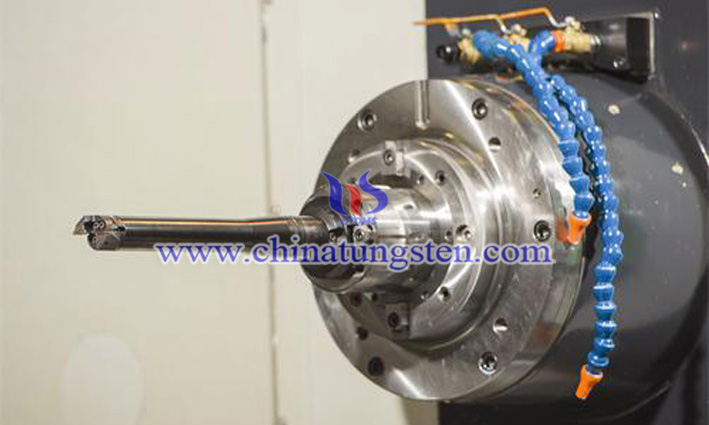
tungsten carbide blade for aerospace picture
Since the success of the first furnace high-temperature alloy trial in 1956, China's high-temperature alloy has gone through more than sixty years in the wind and rain. From scratch, from imitation to independent innovation, the temperature resistance of the alloy is from low to high. Moreover, China's processing technology is steadily improving, and new materials are gradually being developed. In the future, tungsten is very likely to become one of Airfa's formulas. It is reported that China has the ability to independently develop and research new high-temperature alloy materials and new processes, which can solve various high-temperature alloy materials encountered in the production and development of aviation, aerospace and other industrial sectors. The author believes that the creativity of our materials scientists and other scientists is extremely strong, and in the near future, we will achieve more results in the aero engine.